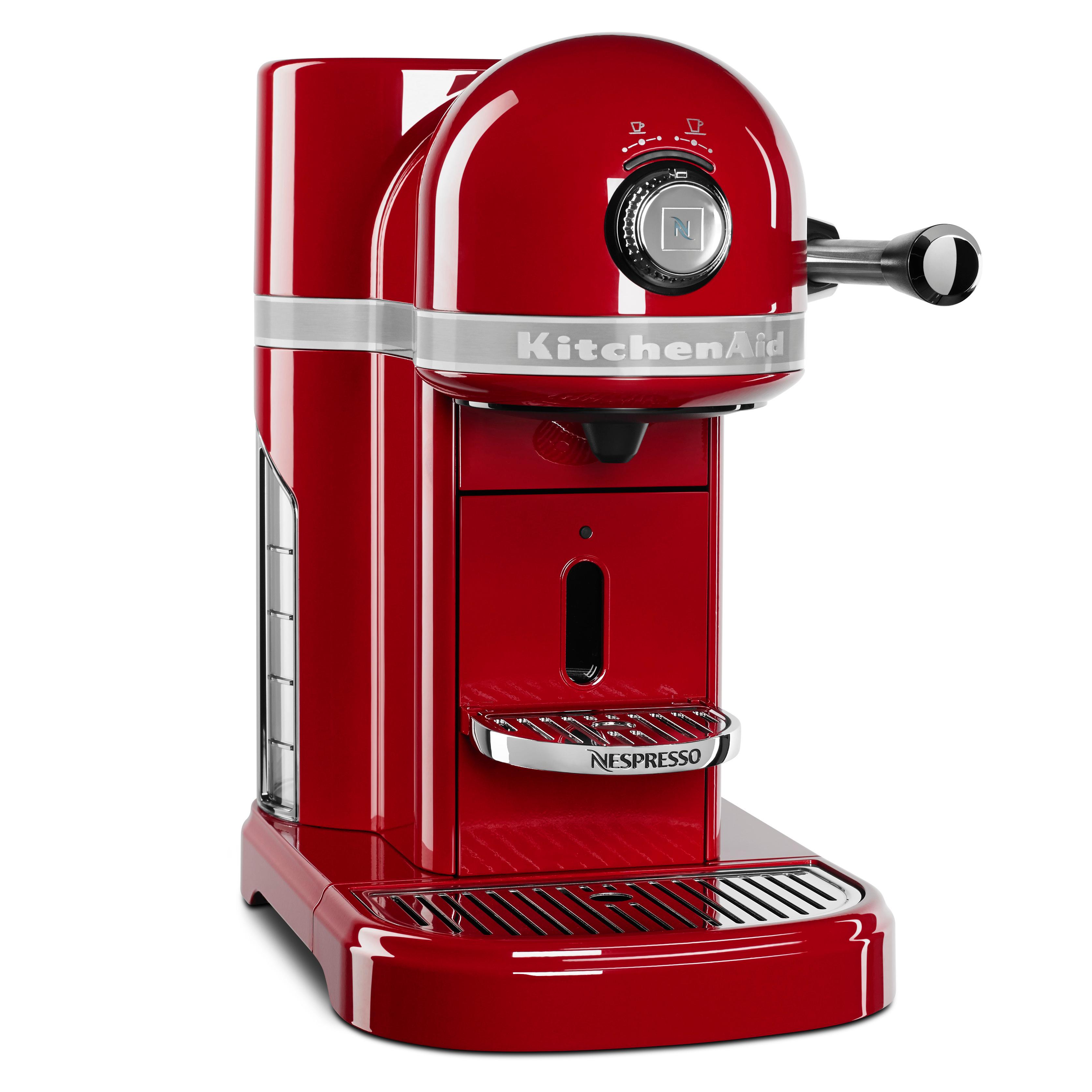
The Artisan Nespresso from KitchenAid marries the high-end design of its metal housing to Nespresso coffee technology. The innovative surface enhancement and the fabulous shaping was achieved using a zinc pressure die-casting process thought through down to the tiniest detail.
KitchenAid Artisan Nespresso: Design with zinc meets gourmet coffee
Its flavor rouses tired spirits. Its aroma delivers a sense of well-being. It boosts concentration and reduces the stress level. Studies show that people who drink up to five cups of coffee a day are less prone than others to cardiovascular disease and to type 2 diabetes. However, and this is to simplify the issue, coffee only used to come from the filter machine, but now the variety and range of choice is enormous. Coffee has now become a lifestyle product, one that is celebrated and enjoyed in all of its nuances – whether simply black, as a creamy latte macchiato, a powerful ristretto or a delicious lungo, either with or without caffeine. Inspired by coffee shops, many coffee lovers are now becoming baristas at home. An increasingly popular method for preparing coffee are automats with a capsule system – such as the Artisan Nespresso, made by KitchenAid.
What is the idea behind it? The coffee is sealed in a small metal capsule, enabling it to remain fresher than the kind sold in pads. Also, the coffee is shot into the cup in much the same way as it is from a real espresso machine. This is intended to filter out the bitter elements from the coffee while at the time delivering a genuine espresso feeling. This assures a most delicious taste in the cup. Not to mention the visual pleasure during preparation. You see, with the KitchenAid Nespresso, high-quality design in a metal housing made of pressure-die cast zinc meets Nespresso coffee technology. Not only that, but the familiar Artisan series is rounded off by its visually striking shapes, all in a hallmark retro design style.
KitchenAid stipulated a set of demanding requirements on design, construction and production: “The surface finish should be of the highest quality, the components should be virtually free of porosity and assembly should be possible without the need for additional machining”, states Darrin Keiser, globally responsible at KitchenAid for the quality management of small appliances, as he recounts the early days of the project back in 2013, “so we went looking for a partner capable of satisfying the challenging quality requirements of our brand”. For months, specialists from KitchenAid and the selected zinc pressure die-casting manufacturer worked away at the details of every single component of the coffee machine to ensure that all requirements were satisfied in terms of visual appearance and functionality.
In a Design for Manufacturing (DFM) feasibility study, the filling and the temperature balancing of zinc pressure-die casting tools were simulated. Darrin Keiser: “To achieve the desired surface quality of the coffee machine, the surface and structure of the zinc pressure die-cast components first needs to be absolutely perfect. The optimum location of the injection points and the overflow was simulated to find out how to prevent air inclusions and porosity, and to ensure that the cavity was getting filled correctly”. During application of the powder coating – an operation during which the zinc pressure die-cast components are heated to about 200°C – the vacuum pressure die-casting process was employed, because it eliminates any formation of bubbles during the pouring process. Through a thorough analysis of tolerances and shapes in each installation position, it was also possible to produce zinc pressure die-cast components on which no rework was required.
The outcome is superlative – and not just visible in kitchens around the world, but also in the absolutely literal sense of the word. At the European zinc pressure die-casting competition in 2016, convened by the International Zinc Association, KitchenAid’s Artisan Nespresso won the title. When explaining its verdict, the expert jury bestowed special praise on the innovative surface enhancement and the fabulous shaping, achieved using a zinc pressure die-casting process thought through down to the tiniest detail.