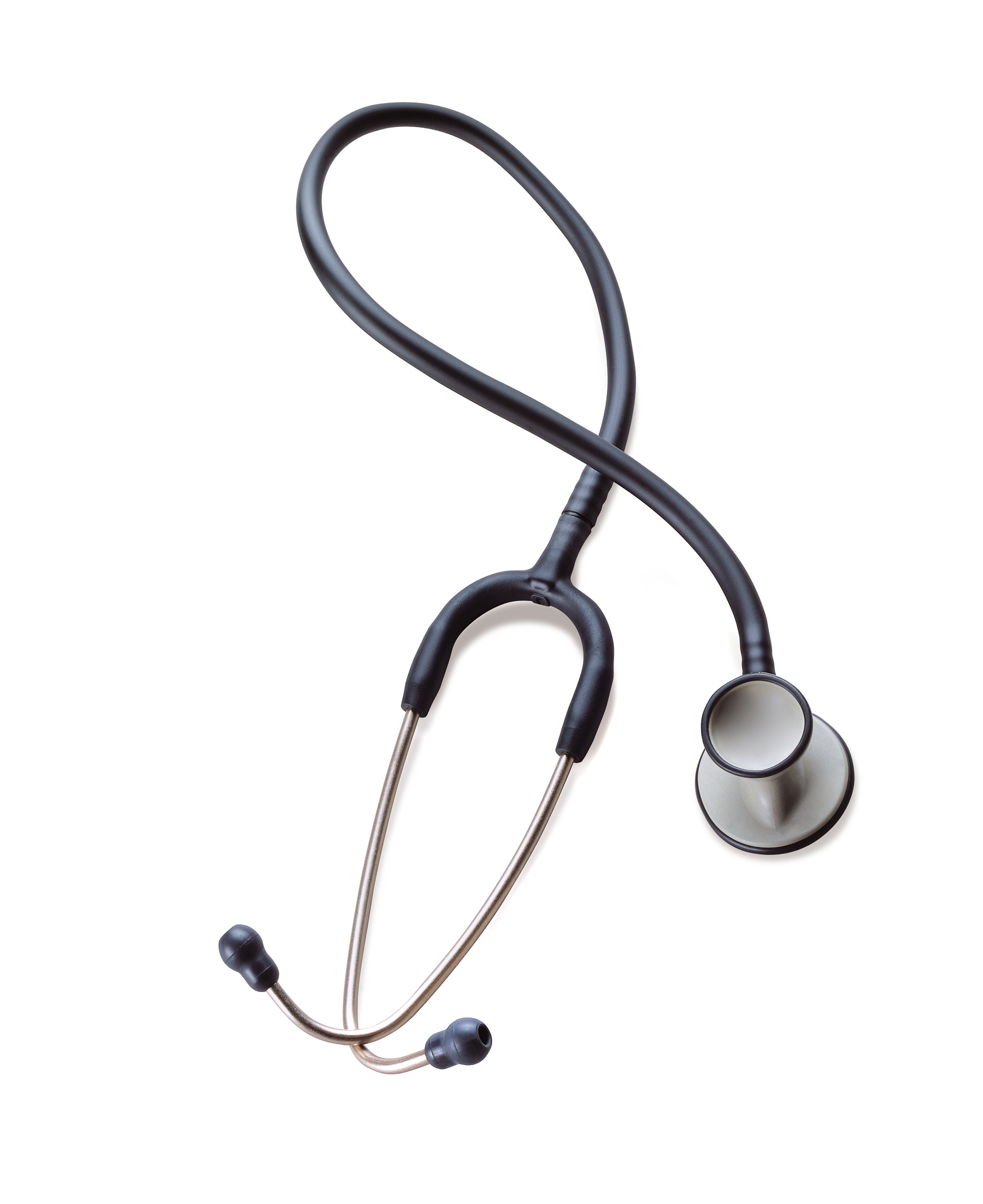
Where precision counts: die-cast zinc in medical and hospital technology
No compromises are permitted when human health is involved. Much depends on the medical specialists and their training and competence. But what really matters is that all the technical equipment used for maintaining and restoring health operates reliably and consistently over long periods. This naturally applies everywhere and at all times. Cutting-edge technology made with first-class materials is rightly expected in Germany, in particular, as a scientifically highly developed country and a technological pioneer in many fields – and it must be available at an economically attractive price. Die-cast zinc is often the ‘hidden champion’ in precision instruments used for internal medicine, ensuring that doctors can concentrate entirely on their patients.
What does die-cast zinc offer?
Die-cast zinc alloys are designer materials characterized by a combination of high mechanical strength, toughness and rigidity, and thus high performance and long service lives, as well as a very good cost-benefit ratio. Their mechanical properties, and the many possibilities of surface treatment, make zinc alloys an effective construction material – in terms of both time and cost. Whether switches, handles, moldings, panels or elements with a technical function – zinc alloys can not only be cast with near-net accuracy in almost any desired shape, but additional precise surface structures and properties can also be integrated during casting, reproducibly adjusting the look, feel and functionality of the product in a defined and targeted manner. Die-cast zinc also offers excellent prerequisites for surface treatments, e.g. galvanic coatings [1], [2], [4].
In terms of accuracy, zinc alloys are almost unbeatable for casting even complex filigree components without machining. In the case of small parts, a reproducible dimensional tolerance of less than 0.03 mm [3] can be maintained – an order of magnitude achieved with modern machines and computer-controlled casting simulations. There are very few processes with which parts can be produced this reliably and this accurately, often making mechanical machining unnecessary. Net shape and zero machining are very great advantages offered by die-cast zinc.
Requirements of medical technology
The above-mentioned precision with which medical devices must always function is undoubtedly one of the outstanding properties that qualify a material for medical technology. There are, however, other properties that also characterize this special field.
Hygiene regulations demand that components that come into contact with humans and their surroundings (i.e. are not located within a machine) must withstand the regular use of detergents and disinfectants without impairing functionality or appearance. The wide range of surfaces that can be achieved with die-cast zinc means that a suitable solution can always be found, even in highly demanding environments. Whenever die-cast zinc parts are used in an aggressive environment, or are intended to meet maximum optical requirements (aesthetics), a wide range and quality of conversion layers, organic coatings or electroplating (e.g. nickel, satinizing and bright chrome-plating) can easily and reliably be used in any desired area of the surface of a die-cast zinc part.
High-quality casting is a basic prerequisite for achieving excellent surfaces. Economical mass processes such as barrel finishing can be used for further decorating the surfaces of zinc parts in their as-cast condition. Extraordinarily smooth surfaces can be achieved with buffing or chemical polishing before surface treatment. The high fluidity of zinc alloys allows particular areas or complete castings to be given defined surface textures in the as-cast state. In addition, writing or logos can be directly molded onto parts.
Medical devices include those that a doctor picks up and manually operates. Examples include dental cameras that doctors move around the patient’s oral cavity, or optical devices used for measuring the human eye in direct proximity. In such cases it is also vital that the device is well balanced, and thus feels good in the hand. It must feel exactly as if the doctor can use it comfortably and thus reliably. Whereby what matters is the weight, balance and feel.
As a result of their high density, and the capability of casting extremely thin walls, die-cast zinc alloys offer designers a high level of freedom, permitting them to deliberately influence the perception of the user regarding weight, balance, quality and inertia. Thus, for example, the ‘cool touch’ (i.e. the typically cold feel of metals) and other sensual impressions are factors appreciated by many users of die-cast zinc. At the same time, however, die-cast zinc parts can, if necessary, also be provided with a warm feel. Whereby ‘warm feel’ coatings or plastic layers are options with which the designer can deliberately influence the feel.
Protection against radiation is an important property whenever radiation is present, e.g. while sensitive electronic devices are being operated. This may involve protecting humans against radiation, such as x-rays. It is also often necessary to prevent the functionality of a sensitive device from being influenced by the electrical or electromagnetic radiation of other devices. Zinc’s screening properties represent a desirable additional benefit for such sensitive situations.
Even in medical technology some technical products are manufactured in high unit numbers. Examples include hospital beds and bedside cabinets. In such cases – in addition to the technical properties of the material – the cost-benefit ratio, i.e. economic efficiency, is of decisive importance.
Where is die-cast zinc used in medical technology?
Die-cast zinc is found everywhere in doctors’ practices and hospitals. As die-cast zinc is either installed within a device (and has a technical function) or has an electroplated surface it is often difficult to recognize die-cast zinc as such. Examples of use include:
•Defibrillators
•Blood pressure monitors
•Stethoscopes
•Bedside cabinets
•Hospital beds
•Infusion stands
•Infusion pumps
•Inhalers
•Devices for artificial respiration
•Ionization units
•Air purifiers
•Portable oxygen supplies
•Pumps for artificial feeding
•Seat lifts
•Monitoring devices
•Wheelchairs
•Crutches and other aids
•Height-adjustable toilet seats
What developments can be expected [6], [7]?
New alloys: The product range for die-cast zinc will increase further in coming years because the material enables the implementation of complex geometries with thin walls whilst maintaining high reproducibility within tight tolerances and retaining its high strength. Flow-filling and mold-filling capacities have been optimized by adapting alloy compositions using grain-refining elements, among other methods, so that maximum quality can be achieved – particularly with very thin-walled components (serially down to 0.3 mm thickness) or high surface demands. Optimized alloys for thin-walled castings and intelligent designs permit weight savings of up to 30% [1], [2], [4].
New casting techniques: New developments, both in casting technology and in surface treatment, show that by no means all the possibilities of zinc have been exhausted:
- Sprue-free and low-sprue techniques increase the resource- and energy-efficiency of the process. The first serial parts are now being cast with these new casting techniques [5].
- A more than 50% reduction in the material required (and thus weight) can be achieved by casting zinc foam using the zinc die-casting process. Although the inside of the casting contains desirable pores, the part has an exterior with a closed surface that can be polished and electroplated.
Prospects for die-cast zinc in medical technology
Forecasts indicate that the use of die-cast zinc in the medical sector will increase in coming years. People are living ever-longer, particularly in the western world. 28% of the population in Germany will be 65 or older by 2030. That is four million people[1] more than today. This development will bring about increased mobile monitoring of health, and greater use of mobile individual measurement and treatment devices. Blood pressure measuring devices and breathing assistance are already widespread today. In future, many other devices are conceivable. Die-cast zinc is the material of choice whenever these devices need to function accurately and have long service lives [8], [9], [10].
Sources
[1] Frank Goodwin and Didier Rollez: ‘Zinc alloys’, Ullmann’s Encyclopedia of Industrial Chemistry, 7th edition, Wiley-VCH 2013
[2] Sabina Grund and Hans-Helmut Jeschke: ‘Zink und seine Legierungen’, Handbuch Konstruktionswerkstoffe, 2nd Edition, Hanser Verlag 2013, Pages 505 – 515
[3] ‘Druckguss aus NE-Metallen’, Technical guidelines. Publisher: Verband Deutscher Druckgießereien (VDD) and German Foundry Association (BDG), edited 2016 version
[4] Sabina Grund: ‘Normgerechte Legierungen als Basis für qualitativ hochwertigen Zinkdruckguss’, Giesserei Praxis, Issue 4/2014
[5] Sabina Grund: ‘Ressourceneffiziente Gießtechniken beim Zinkdruckgießen’, Giesserei, Issue 9/2016, Pages 36 – 38
[6] Homepage Initiative Zink: http://www.initiative-zink.de/basiswissen/das-metall-zink/zinkdruckguss/
[7] Homepage of the International Zinc Association: //diecasting.zinc.org/
[8] Didier Rollez: ‘Zinc die-casting in Europe – new developments’, presentation at the 1st International Zinc Conference Europe, Brussels 8 – 10 May 2017
[9] Frank Goodwin: ‘Future uses of zinc’, presentation at the Short Course on Zinc as part of the PbZn Meeting 2015, Düsseldorf 15 – 17 June 2015
[10] German Federal Statistical Office 2015, https://service.destatis.de/bevoelkerungspyramide/#!y=2031