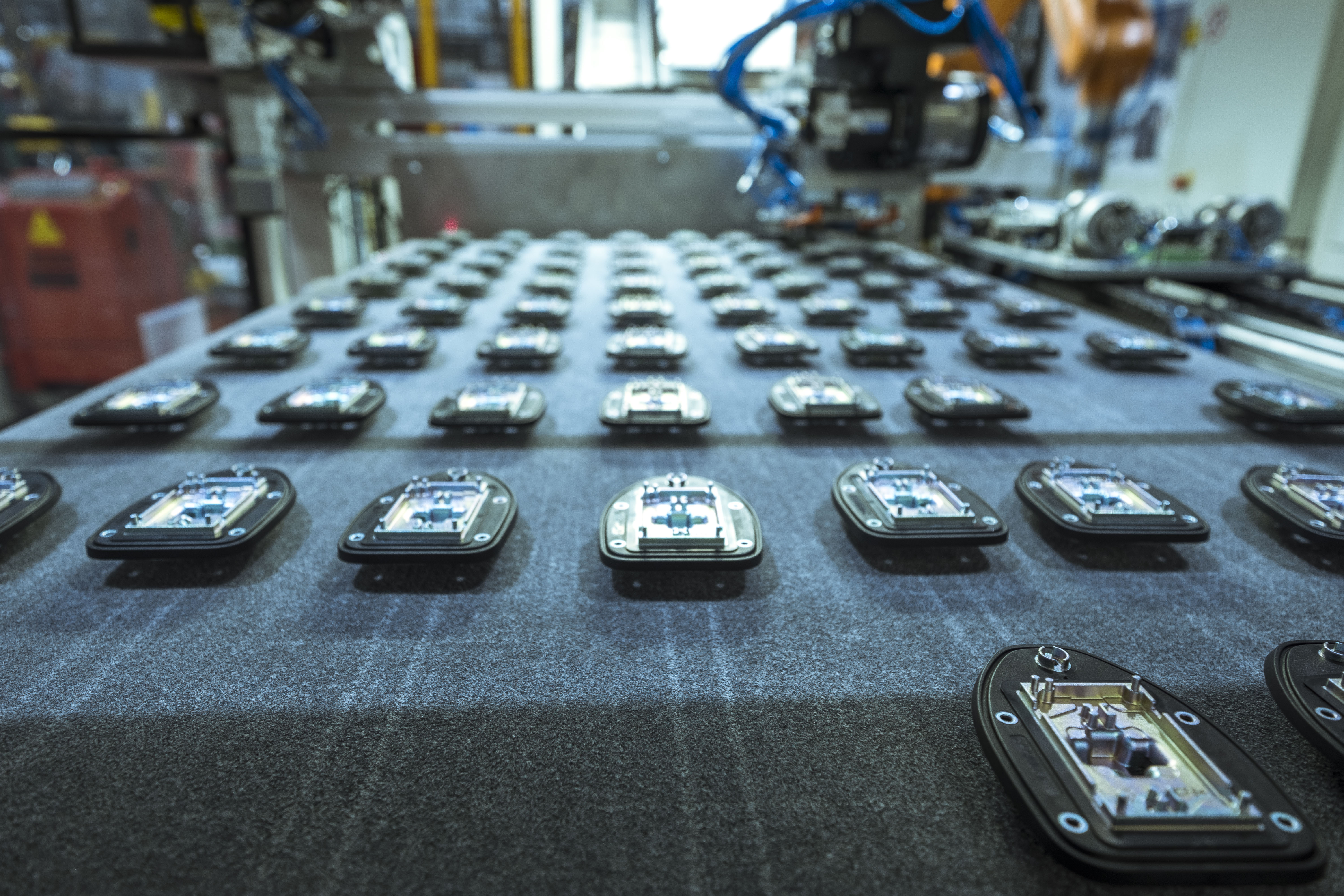
Small, large, filigree, thin, fast – zinc pressure-die casting is the answer to these challenges
The pressure die closes – then is filled with liquid melt under high pressure, defining the complete shape of the resultant component in technological and metallurgical terms. This entire process takes place in just 10 to 20 milliseconds and is therefore virtually imperceptible to the human eye – bearing in mind that a single blink takes no fewer than 100 milliseconds. Simplified very roughly, the most important step in the zinc pressure die-casting process can be described like this, and nothing fundamental has changed in this process since it was invented back in the early part of the 20th century. Note that wording though: “nothing fundamental”. You see, like every process, zinc pressure die-casting has proven over the last few decades just how much potential it conceals for enhanced performance and innovation. Or, as Petar Marovic, the senior shareholding partner at Havelländischer Zink-Druckguss GmbH & Co. KG, puts it: “Most of the characteristics of the zinc pressure die-casting process have not changed significantly. However, this is no expression of any lack of drive to innovate. Instead, it shows that the process has already achieved a certain optimum level that can only be improved upon at a nuanced level.
Remaining on the subject of best times and records, simply going for Bigger, Faster and Further – along the lines of the Olympian concept – does not express the defining criteria governing zinc pressure die-casting: “If you look at the requirements of modern zinc pressure die-casting products, fast production and the creation of large components also have a role to play. Furthermore, it is very important to create components that are thin-walled, small and filigree, that often exhibit a high propensity for functional integration, that are visually superlative and yet can still be manufactured quickly, efficiently and to a high standard of quality. All of these requirements have changed the zinc pressure die-casting process – and can be achieved with it. For this, we have modern pressure die-casting machines as well as innovative process technologies”, explains Dr. Norbert Erhard, the CEO of Frech GmbH & Co. KG, a company involved in various business sectors, particularly in the manufacture of hot chamber and cold chamber pressure die-casting machines, tool technology and the automation of pressure die-casting cells.
Man, tool, material, machine and process: These five criteria constitute the success team for a high-performance zinc pressure-die casting process that incorporates a high level of innovation. To enable zinc pressure die-cast components to be integrated perfectly in their respective fields of application, strict standards apply to all stages from tool building to production. Many parameters are taken into account, including the choice of material , shrinkage of the pressure die-cast component, the design configuration of the die and process stability. All of which ensures that the final result is a good one, and that subsequent rework is not needed. “The quality of a component is determined in the tool to between 60 and 70 percent. Specialists in Engineering and Design are being called upon to find an intelligent component design that ensures that challenging geometries can be cast to maximum precision and optimum quality standards – Man is at the heart of the entire process”, emphasizes Dr. Frank Kirkorowicz, senior managing partner of Adolf Föhl GmbH + Co KG.
Keyword “Material”: In practice, it is especially the alloys ZL 0400 (Zamak3), ZL 0410 (Zamak5) and ZL 0430 (Zamak2) that have established themselves. These are based on fine zinc with a purity level of 99.995 percent zinc. Aluminum, copper and magnesium are other ingredients that play a defining role in the characteristics profiles of these alloys: Copper improves tensile strength and hardness while magnesium prevents intercrystalline corrosion and aluminum enhances the processing capabilities of zinc as well as the most important properties for use, including tensile strength, failure strain and flexural impact strength. “The fact that zinc pressure die-casting works primarily with just three alloys is of course very convenient”, states Frank Kirkorowicz, “Although even more applications are possible with optimized alloys – especially when you consider the electronics sector, for which components need be designed with much thinner wall sections”. For this, what are known as high-fluidity alloys are used that were developed specifically for thin-wall castings, and that exhibit the same good mechanical, electrical and thermally conductive properties as classic alloys, but that have flow characteristics that are up to 40% more effective. Dr. Erhard: “Back in the Nineties, wall thicknesses of 1.5 mm were state-of-the-art, but now, through improvements to the process, a standard thickness of 0.5 mm can be achieved. Nonetheless, development work here is going even further, to the extent that now 0.3 mm or even 0.2 mm can be implemented with this technology.
Efficiency and innovation in machine and process technology are other central topics that need to be mastered precisely if performance standards are to be improved yet further in zinc pressure die-casting. Simulations of die filling and solidification constitute a preliminary stage that reflects volume production conditions even before the building of a tool. This makes it possible to estimate how the cast product will behave – taking account of various variables such as temperature and air resistance. To produce a prototype, 3x D-pressure is always set. However, it is in precisely this area that Petar Marovic sees further scope for development: “In the field of small quantities, the step from rapid prototyping to additive manufacturing has already been successful. This is where the latter has been showcasing its strengths, where a high level of design freedom, functional optimization and integration with exceptionally complex structures is required in conjunction with light weight and stability. What this means for alloy manufacturers is this: Getting zinc fit for additive manufacturing and marrying development work to that same goal in good time.
And what of the pressure die-casting machine itself? Frank Kirkorowicz: “The pressure die-casting machines today are easier and more accurate to operate, and this helps to assure a high level of process repeatability. The development of control, monitoring and display systems for pressure die-casting machines have made enormous strides forward. For example through the use of sensors in the tool that enable accurate deductions to be made about the production of precise contours. Milestones include casting with only small sprue, or none at all, and real-time feedback control that enables the unit to be braked accurately while still retaining the shortest possible die-filling times. While the notion of machines that can adjust themselves by means of algorithms may still be looking ahead somewhat, it will become possible in the near future”. Norbert Erhard adds “Pressure die-casting machines have to be able to do more today than simply cast. By way of example, it is also important to conserve resources. The avoidance of sprues makes it possible to save at two locations: firstly, less material is needed in the pressure die-casting of the product, while on the other hand, less to no material is affected by recycling because there is almost, or even absolutely, no casting residue. This is turn translates into a substantial gain in productivity – while at the same time reducing energy consumption and therefore also reducing the emissions of carbon dioxide”.
Bigger, smaller, more filigree, thinner, faster – in all of these production disciplines, zinc pressure die-casting scores highly – and in an extended sense, it can scale the winner’s rostrum. Today and in the future. The list of existing and possible future fields of application is a long one. Just take a look at the automotive industry: Although the proportion of zinc pressure die-cast products in a European automobile has declined from 23 to 21 percent, the number of zinc pressure die-cast components has almost doubled. “Another fast-growing market is the electronics sector – regardless of whether you are looking for intelligent solutions for your home or for the electric car”, states Petar Marovic, “Nowadays every small car has more control units and communication interfaces that luxury cars did ten years ago, and house automation and control are also gaining in significance – and across the board here, zinc pressure die-casting will also follow suit”. An appraisal shared by Frank Kirkorowicz: “In the e-mobility and Smart Home sectors, security and networking capability are important factors. Individual components are becoming ever smaller and more precise. Zinc pressure die-casting can score highly here – especially in these sectors where large quantities are involved – and where it is increasingly becoming the production process of choice.